- CAD detailing for sheet metal fabrication firms is a daunting task when done in-house with limited resources.
- Collaborating with an offshore expert in CAD drafting and modeling help overcome any shortfalls with efficiency and quality.
- HitechDigital teams have delivered excellent CAD drafting and sheet metal fabrication drawings for global sheet metal fabricators to stay profitable.
CAD detailing is complex, especially for firms with limited resources. Sheet metal fabricators who struggle with a lack of detailing capabilities face severe issues, affecting their work quality, productivity, and ability to compete.
Small or new sheet metal fabrication firms, in particular, find CAD detailing difficult. They often miss important industry practices and rely on outdated paper drawings. This causes inefficiencies in their designs.
Understanding material types and manufacturing processes is difficult and can cause delays and the need for frequent design changes. Common challenges include incorrect interpretation of design elements such as bend radius, k-factor, and hole positions in different thicknesses of metal sheets. These issues lead to fabrication errors and work interruptions to make corrections.
CAD service providers help significantly overcome these challenges. They provide expert help, improving the fabricators’ speed, work quality and cost-efficiency. While there are numerous factors that help decide your outsourcing partnership, we have prepared a list of top 10 factors you should consider to choose a sheet metal CAD drafting partner. Here are HitechDigital’s three success stories for sheet metal design detailing that showcase our CAD design drafting support to global sheet metal fabrication companies.
Table of Contents
Role of CAD detailing in sheet metal fabrication
Currently, the sheet metal fabrication industry is undergoing a significant transformation. All thanks to the large-scale adoption of CAD and Design for Manufacturability and Assembly (DFMA) principles. CAD detailing and DFMA streamline the entire fabrication process.
Implementing CAD detailing brings the following benefits:
- Accuracy and precision
- Improved efficiency and ROI
- Cost optimization
- Automation and visualization
- Flexibility and customization
Three projects of CAD drafting by HitechDigital in sheet metal fabrication
Now, let’s explore through three success stories of how sheet metal CAD detailing by HitechDigital Solutions empowered businesses across industries to achieve their goals.
Case Study 1: Reduction in 50% Design Iterations with CREO Top-down Parametric Approach
The first project involved an Irish company specializing in recycling and material waste-handling equipment. The client aimed to enhance existing designs and develop new ones for walkways, support structures and hoppers to streamline material handling. Let’s see how HitechDigital Solutions embraced the client’s demands with CREO.
Primary Challenges Faced by the Client
Our expert team identified the following challenges that the client faced in achieving their target.
- Complex Design Iterations: The intricate nature of industrial equipment design, especially in hoppers, poses multiple challenges. It demanded meticulous detailing and frequent design changes.
- Resource and Process Challenges: Heavy CAD files, design interdependencies, and the complexity of existing plant models pose significant challenges, necessitating a revamp in the design and manufacturing process.
What We Did:
We responded to the client’s concerns and objectives with:
- Top-down Parametric Approach in CREO: HitechDigital introduced a top-down parametric approach in CREO. The innovative top-down approach, followed by our engineers, facilitated the creation of plant assembly models with embedded sheet metal designs. Additionally, it allowed the simultaneous development of assembly and parts, streamlining design changes.
- Stringent Quality Audits: To ensure adherence to standards, HitechDigital implemented rigorous quality audits. Our team always strictly complies with industry standards like ANSI, TEMA, and DFMA principles. This included checks for material thickness, clearances, clashes, and sheet size limits, contributing to the production of error-free designs.
- Collaborative Design Approach: The collaborative approach involved sharing input models and design concepts with the project team. A team of four CREO engineers from HitechDigital worked on manufacturing ready models, addressing the resource challenge.
Impact and Results:
Project Samples:
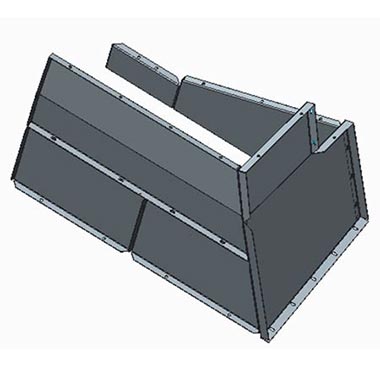
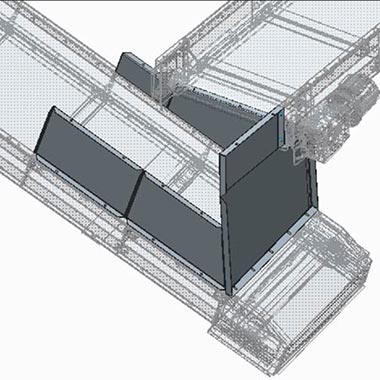
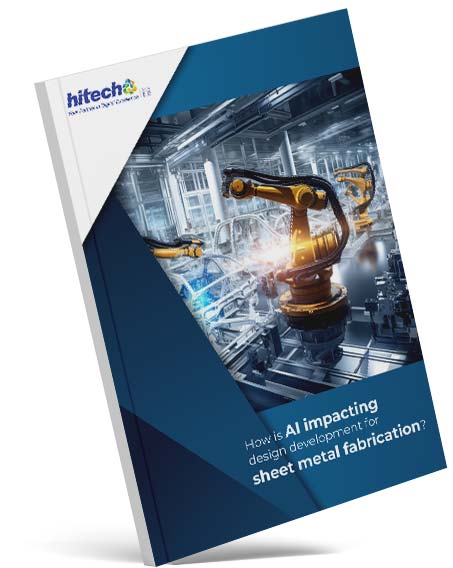
How AI is impacting design development for sheet metal fabrication
- Optimize CAD design process with AI for metal fabrication
- Accelerate prototyping; ensure quality and compliance with AI
- Reduce scrap and minimize environmental footprint
Case Study 2: Accelerated Turnaround Time with Drawings and Models as per DFMA Guidelines
The second project involved a business that faced challenges in accommodating fluctuating market demands and requiring flexibility in resources and capabilities. It required skilled CAD engineers to provide 3D models and 2D drawing files for various fabrication operations, incorporating Design for Manufacturability and Assembly (DFMA) inputs.
Primary Challenges Faced by the Client:
Our expert team identified the following challenges that the client faced in achieving their target.
- Input File Format: Initial inputs in the business were provided only in PDF files, leading to iterative work for accuracy in design detailing.
- Complex Assemblies: Heavy and multi-component assemblies were employed, requiring multiple resources for effective handling.
- Manufacturing Detail Accuracy: With diverse design requirements, it was hard to maintain precision and key detailing in the project.
What We Did:
We responded to the client’s concerns and objectives with:
- Communication and Clarification: The first thing we focused on was clear communication. Upon receiving the PDF drawings, the team defined the scope of the work and initiated the development of manufacturing drawings. Later, initial calls were set up to address queries related to tooling capabilities and other Requests for Information (RFIs) in input drawings.
- Correction of Design Details: The client found it hard to adjust to diverse designs. Thus, corrections and new drawing developments were made, sometimes with the receipt of SolidWorks and other CAD models.
- Parametric Modeling: Based on previous experience with DFMA guidelines, the team began with sheet metal modeling in SolidWorks. 3D parametric models were developed with a top-down approach for repetitive products, enabling the interlinking of parts and assemblies to auto-update properties and design parameters.
- CAD Library Development: The team gradually built a library of product mixes for the client, with about 70% of the product library readily available after three months. This helped minimize time consumption. Also, the final sheet metal fabrication drawings, including parts and assemblies, were quality-checked against a checklist before being shared with the client through secure email.
Impact and Results:
Project Samples:
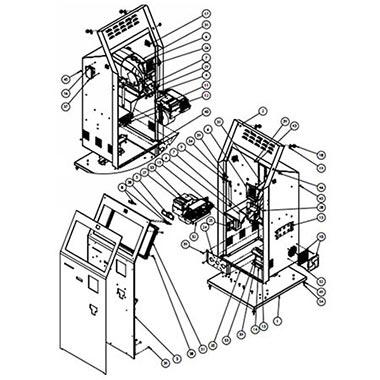
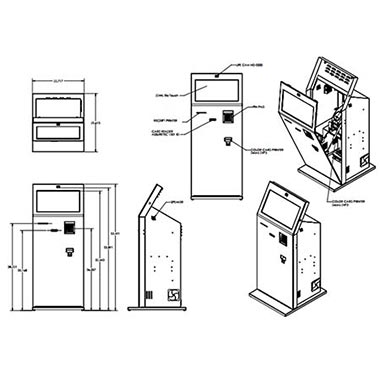
Case Study 3: 3D CAD Modeling Redefining Drawing Output
This project revolved around a leading manufacturer of large-sized steel structures based in Russia, operating in the Fabricated Structural Metal Products (FSMP) industry, where deadlines and quality needed to be met utilizing fewer resources.
Primary Challenges Faced by the Client:
Our expert team identified the following challenges the client faced in achieving their target.
- Data Extraction Complexity: It was difficult for the client to read and organize part details from complex 2D PDF drawings.
- Time Constraints: Short turnaround time between input receipt and final drawing release.
- Resource Shortage: The client had limited resources and the ability to deliver quality and cost-effective CAD solutions.
What We Did:
We focused on the following to address the client’s concerns and objectives:
- Efficient Information Extraction: Our team of experts at HitechDigital extracted accurate information along with the right dimensions from information-rich 2D PDF drawings.
- Faster Modeling: Later, as in the other two cases, we worked on the modeling part. But unlike other cases, here we employed a bottom-up modeling approach for the swift creation of 3D part models and steel structure assemblies. That shows our ability to customize approaches as per the client’s requirements.
- Collaborative Issue Resolution: We believe in establishing transparency and prompt communication with our clients regarding discrepancies. Further, we resolve the queries and issues within a day to maximize work output.
- Quality Assurance: Before making a final submission, we verify final assemblies against a QC checklist. That results in quality final products and client satisfaction at the end of the cycle.
Impact and Results:
Project Samples:
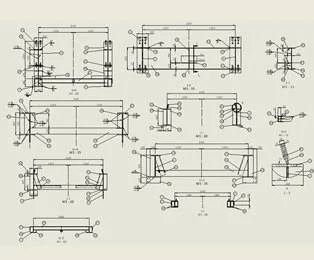
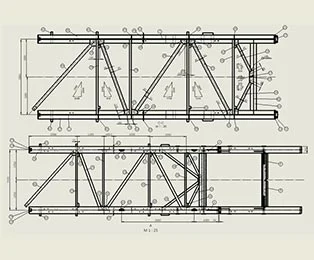
Conclusion
As the sheet metal fabrication market continues to grow, CAD detailing will gain in importance. With fabrication products becoming more complex, and designers trying out new material combinations with the latest tools, the translation of design to product will heavily depend on the quality of CAD detailing. However, skilled resources would also become more difficult to find and employ as individual CAD experts, and finding reliable CAD service providers might become the best option for small sheet metal fabricators struggling with CAD detailing.
Maximize your sheet metal fabrication efficiency
Partner with the best sheet metal CAD drafting team