- By representing physical spaces with data-rich 3D digital models Scan to BIM technology enables informed decision making while improving communication, cost estimation, and planning. Adoption of Scan to BIM technology is influenced by data complexities and integration issues.
- Technological breakthroughs like drone-based scanners, autonomous indoor scanning, and predictive modeling are transforming Scan to BIM use.
- Standardization, training, and quality control are key to navigating Scan-to-BIM challenges and unlocking its complete potential.
Scan to BIM (Building Information Modeling) technology is transforming the construction industry by improving project accuracy, efficiency, and collaboration. It uses 3D laser scanning to create detailed digital models of existing structures and helps address critical and persistent industry challenges related to as-built surveys and clash resolution.
Table of Contents
Scan to BIM services streamline design, optimize construction, and minimize risks for successful projects. Scan to BIM enhances accuracy by capturing precise measurements, reducing errors, and rework during construction. It also promotes collaboration by providing a unified digital platform for various stakeholders to visualize and interact with the updated 3D model, streamlining communication, and project execution.
Despite its benefits, Scan to BIM adoption faces challenges. This article explores these challenges, strategies for overcoming them, and emerging advancements in Scan to BIM technology.
Significance of Scan to BIM in the AEC sector
Scan to BIM is not just about new construction; it has revolutionized renovations. Accurate capture of the existing conditions of a building, including structural elements and hidden infrastructure, enables faster planning and ensures minimal disruptions. A data-driven strategy lowers the risk of challenges and drives sustainable and cost-effective renovations and remodeling.
As tools and technology continue to transform processes, Scan-to-BIM has become more accessible. The use of AI and ML has further enhanced the capacity of Scan-to-BIM and its application for task automation, object recognition, and classification.
Optimize your workflows with Scan to BIM.
Get precise as-built models fast, with +/-10 mm accuracy for your projects.
Scan to BIM adoption challenges
Cost limitations
Initial investment in 3D laser scanning software and equipment is a barrier for small firms with limited budgets. Furthermore, the need for skilled technicians to utilize tools and process data drives another layer of expenses. The time-consuming nature of data modeling and processing creates a financial strain on project schedules and resources.
Lack of awareness
Lack of understanding on potential applications and benefits of Scan to BIM tools can impede extensive adoption. AEC professionals may not understand how these tools can enhance accuracy, streamline workflows, and lower costs, leading to unwillingness to adopt.
Integration problems with BIM workflows
Integration existing BIM workflows with Scan to BIM data can be challenging based on compatibility issues between data formats and software platforms. This consumes time for data conversions and potential information loss that impedes seamless collaboration between project participants.
Scanner selection and data acquisition
Selecting appropriate 3D laser scanning equipment for a specific project is overwhelming based on the availability of multiple options with diverse pricing and capabilities. Data acquisition can be time-consuming and requires meticulous planning for complete coverage and required scan density.
Data processing and noise filtering
Processing large point cloud datasets from 3D laser scanners is computationally intensive, and requires high-performance hardware and software. The presence of noise in raw scans affects data accuracy and quality of 3D BIM models, and requires additional cleaning and filtering.
Modeling and object recognition
3D Scan to BIM conversion can be challenging due to the difficulties in creating precise and detailed 3D BIM models with complex geometry and intricate details. Object recognition algorithms often struggle to accurately identify and classify building elements, necessitating manual corrections.
Defining appropriate LOD
Determining appropriate LOD for Scan to BIM can achieve accuracy and detail. High LOD’s provide high precision, but need more effort and time, while lower LOD’s would not capture required information for certain projects or applications.
Storing and managing large 3D Point Cloud data
The volume of 3D Point Cloud data generated by 3D laser scanners is storage and infrastructure intensive. Accessing and managing data can be challenging based on traditional file formats and data structures that are not enhanced to handle such large datasets leading to bottlenecks in analysis and data processing.
Minimize costly errors and rework with optimized Scan to BIM processes.
Unlock the precision of digital twins for flawless project execution.
How to overcome Scan to BIM implementation challenges
1. Perform detailed planning and preparation
Before starting the scanning process, a detailed project plan needs to be established.
It includes definition of direct project goals, identification of required deliverables (e.g., architectural design with LOD 300), and outlining work scope.
Understanding the use of BIM can support customization of the scanning process for each project. Moreover, identifying potential challenges, such as occlusions within equipment or furniture, hard-to-reach crawl locations, and lighting conditions, can improve the planning process. Creating preemptive strategies can remove challenges early to save resources, time, and costs in the long run.
2. Select the right scanner and point cloud to BIM software
Selecting the right 3D laser scanner and Point Cloud to BIM software is imperative for the success of a Scan-to-BIM project.
Factors like accuracy, scanner speed, range, and compatibility with the selected software. For example, for a large-scale project such as industrial facilities, long-range scanners with high accuracy would be the preferred equipment.
Conversely, for a smaller location, portable scanners are appropriate. It is critical to invest in software that can handle large point cloud datasets, provide powerful alignment tools, offer robust registration, and integrate with BIM platforms.
3. Prioritize the quality of data
High-quality data scans set the foundation for Scan-to-BIM. Ensuring optimal data quality, utilizing consistent lighting, reducing vibrations by controlling the scanning environment, and capturing overlapping scans ensures high data quality.
Deploying a strong QC process for the entire scanning procedure can produce deliverables with the required resolution and detail. This would require software to identify and flag outliers, check registration issues, and inspect point clouds for inconsistencies. Addressing issues with data quality can help avoid reworks in the project.
4. Achieve effective collaboration
As Scan to BIM projects involve various stakeholders like modelers, designers, and surveyors, it is crucial to implement collaboration workflows and tools to achieve common goals and resolve challenges.
Establishing channels for clear communication that include regular meetings, project management software, and cloud-based platforms encourages feedback and open communication to facilitate a collaborative environment. This helps resolve ambiguities between design intent and scanned data, or differences of opinions on the Level of Detail (LOD) required for specific components.
5. Invest in expertise and training
Scan to BIM workflows can display complexities. This requires domain knowledge and technical skills from the team for laser scanning, processing point clouds, and 3D BIM modeling.
Providing the required training on specific tools or Point Cloud to BIM software can help navigate complex projects to ensure winning project outcomes. If the in-house team lacks expertise, partnering with the external Scan to BIM service providers can be considered.
6. Use Scan to BIM automation
The use of automation streamlines the Scan to BIM process through the reduction of manual effort and expedited project schedules.
Identification of repetitive tasks, including noise reduction, point cloud registration, and feature extraction with multiple software solutions enriched by automation, can improve project accuracy and quality. It is crucial to deploy quality checks for workflow automation to ensure precision and error mitigation.
7. Ensure optimal object and model recognition
To achieve accuracy within model and object recognition in Scan to BIM, it is critical to ensure standardization and best practices.
Consistency in scanning techniques, and maintaining consistency in resolution, settings, and overlaps ensure uniformity in data quality. Removing noise with data preprocessing, outliers, and other objects improves the algorithm’s object recognition accuracy and mitigates errors in the 3D BIM model.
Deploying semantic segmentation helps classify point cloud data into categories for automated object recognition and the creation of precise BIM models. Using a standardized library of BIM objects accelerates 3D modeling and ensures consistency. Using ML algorithms on vast point cloud datasets helps identify complex objects and structures within scan data.
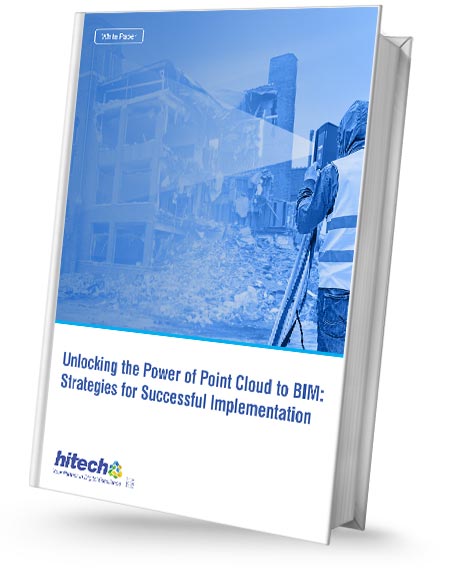
Learn how Point cloud to BIM can streamline your building processes.
- Establish an accurate geospatial context for point cloud data.
- Simplify and optimize mesh representations of point clouds.
- Implement rigorous quality control procedures throughout the process.
- Adopt an iterative approach to modeling based on ongoing analysis.
Preserving architectural heritage of a 16th-century UK monument with Scan to BIM
A UK-based surveying firm approached HitechDigital to create 3D BIM models for retrofitting a 16th-century heritage monument spanning 580,000 sq ft. Understanding BIM LOD 100 to 500 was crucial for this project, as it required creation of a LOD 400 model, which involved high-level detailing, including fabrication, assembly, and installation information. The project also demanded careful preservation of the monument’s architectural features, which is a key consideration when working with heritage structures.
The BIM team converted the input Point Cloud scans into a 3D BIM model, creating geometries, shapes, and extrusions. Parametric Revit families were included within the 3D model, and structural components like beams and columns were created. Various QA/QC processes were implemented with error checklists to ensure the accuracy and validity of the scan to BIM process and 3D model.
The project was completed within two months and helped enhance decision-making for scheduling and material takeoff.
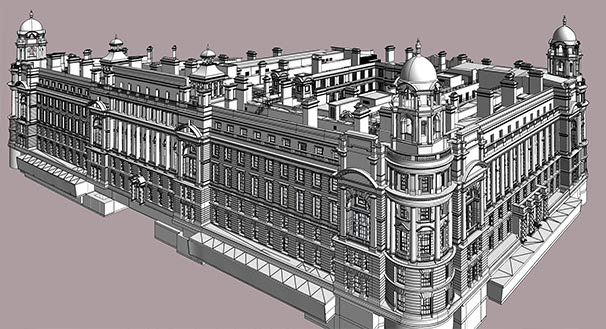
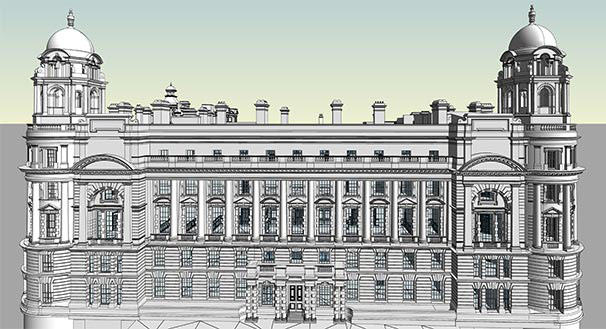
Benefits of using Scan to BIM technology
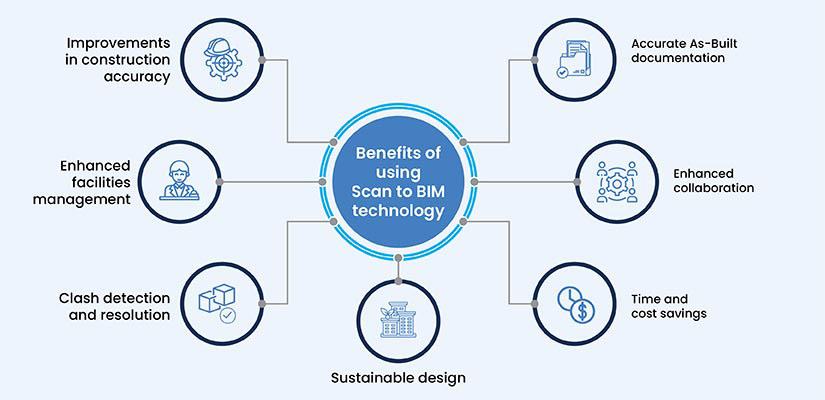
Breakthroughs and Emerging Trends in Scan to BIM technology
Artificial Intelligence (AI) and Machine Learning (ML)
-
Automated Object Recognition:
Machine learning (ML) models are trained for automated object recognition on large point cloud datasets, identification, and categorization of architectural elements like windows, doors, and structural objects. Automation within Scan to BIM reduces the manual effort required for 3D BIM model creation and leads to greater Scan to BIM accuracy and efficiency.
-
Semantic Enrichment:
Semantic enrichment moves beyond mere geometry and includes assigning rich data to objects within the 3D model. Analysis of point cloud characteristics like intensity, color, algorithms, and patterns can assign attributes like thermal properties, structural classifications, and material types like wood, concrete, and glass.
Semantic enrichment improves the value of 3D BIM models. Engineers and designers can gain deeper insight into building elements for improved decision-making during various stages like design, construction, and maintenance. Gaining scan-to-BIM accuracy within material identification leads to sustainability analysis and cost estimation.
-
Predictive Modeling:
Predictive modeling is a powerful tool in design, construction, and renovation. Harnessing the capabilities of Artificial Intelligence (AI) helps in the analysis of As-Built data to forecast potential problems in construction or renovation.
The proactive strategy allows teams to flag clashes between existing components, plan modifications, anticipate weaknesses, and improve material use. Identifying and resolving potential issues in early design with predictive modeling can prevent delays, mitigate rework, and unforeseen issues.
Integration of Reality Capture Technologies:
-
Drones and UAVs:
UAVs and drones have transformed data collection for large-scale and hard-to-access projects. Equipped with advanced cameras and sensors, they capture high-resolution images, enabling efficient creation of accurate point clouds for Scan to BIM models. These technologies are invaluable for surveying large construction sites and monuments, capturing intricate details, identifying hazards, and reducing the need for manual surveys and scaffolding.
-
Mobile Mapping Systems:
Mobile Mapping Systems (MMS) integrate laser scanners with precise positioning systems like IMUs and GNSS, enabling efficient data acquisition in dynamic spaces. Mounted on backpacks, handheld devices, and vehicles, MMS accelerates 3D point cloud data capture. Ideal for surveying roads, urban landscapes, and infrastructure, MMS provides geo-referenced data for applications such as asset management, 3D mapping, and infrastructure tracking.
-
Indoor Mapping Robots:
Indoor mapping robots, equipped with 3D scanning and LiDAR, autonomously collect accurate point cloud data within interior spaces. They offer consistent, uniform scanning, reducing human error. These robots navigate complex environments to create precise Scan to BIM 3D models, digital twins, and documentation for facilities management, enhancing efficiency, data quality, and safety for AEC and Facilities Management.
Conclusion
Scan-to-BIM is becoming improved and more accessible due to technological breakthroughs that help address challenges in its adoption. While roadblocks like data complexities and integration continue, solutions like cloud-based collaboration and AI-driven automation are setting higher standards for extended BIM adoption in the AEC.
As the AEC industry advances, the use of Scan-to-BIM workflows will continue to grow due to their unique advantages.
Unlock the power of BIM for renovations and retrofits.
Capture complex geometries and streamline your design and construction processes.